Factory Automation Solution in Malaysia: Technologies, Providers, and Market Outlook (2025)
Factory automation solutions in Malaysia are essential to the country's industrial competitiveness and digital transformation strategy. As manufacturing evolves under Industry 4.0, local and multinational factories are increasingly adopting automation technologies to improve efficiency, consistency, and cost control.
This article explores factory automation in Malaysia, key technologies in use, benefits of automation, supplier selection considerations, and the market trajectory through 2025 and beyond.
What Is a Factory Automation Solution?
Factory automation refers to the integration of technology systems that automate industrial processes with minimal human intervention. A factory automation solution combines hardware, software, and control systems to improve productivity, accuracy, and safety across production lines.
Typical components and technologies involved in factory automation include:
- Programmable Logic Controllers (PLCs)
- Human Machine Interfaces (HMIs)
- Industrial sensors and actuators
- Servo motors and drives
- Robotics and automated material handling systems
- SCADA and Manufacturing Execution Systems (MES)
- Vision systems and quality control automation
Applications of Factory Automation in Malaysia
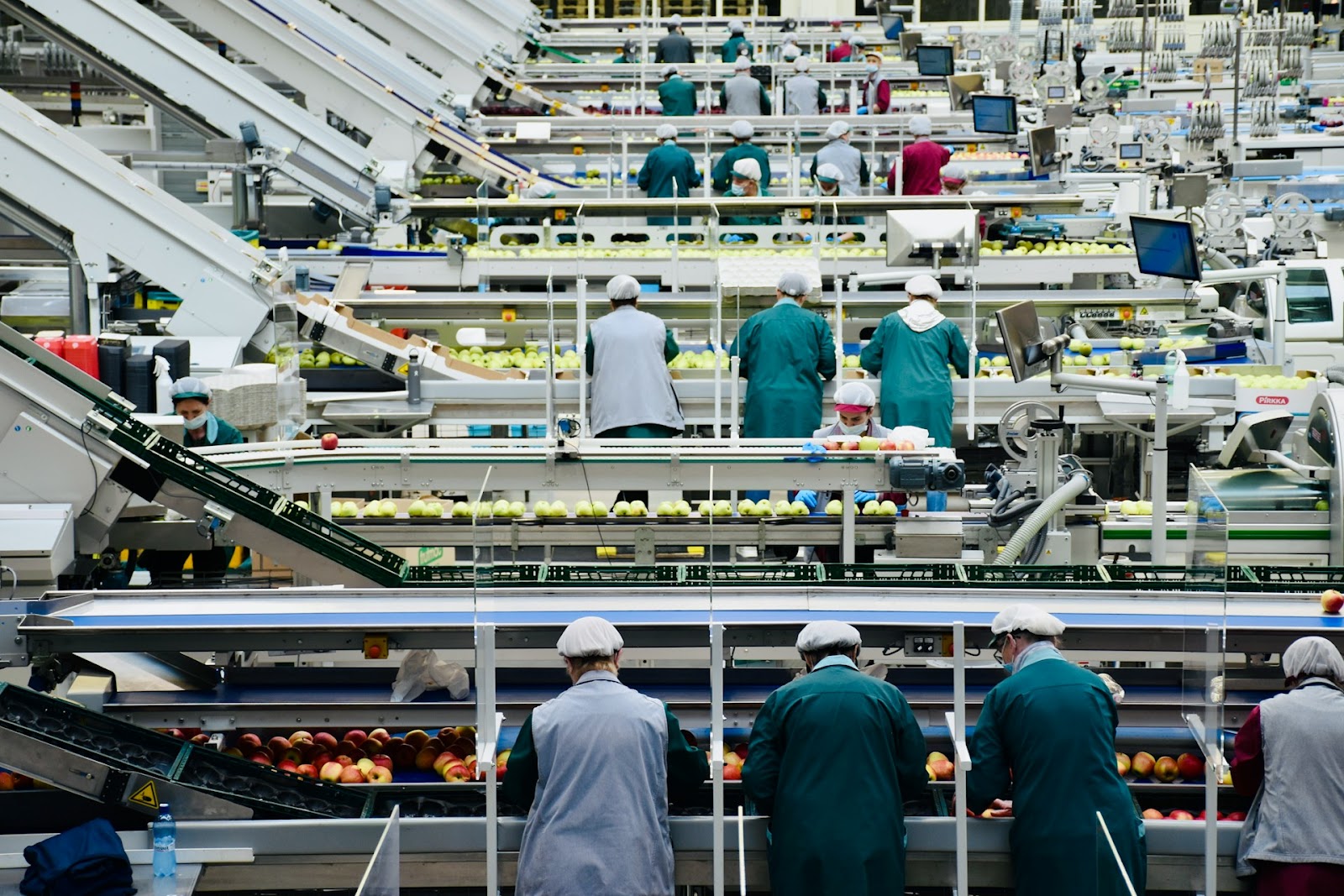
Factory automation plays a key role across multiple sectors in Malaysia, helping companies enhance productivity, consistency, and quality while reducing reliance on manual labour. Here are some of the major industries driving automation adoption:
Electronics and Semiconductor
Malaysia is a global hub for electronics assembly and semiconductor testing. Automated systems are used for pick-and-place machines, SMT (surface mount technology) lines, wafer handling, and cleanroom robotics, especially in Penang and Selangor-based facilities.
Automotive and Components
Automation is deployed in welding cells, painting booths, conveyor-based body assembly, and inspection stations. Automation improves cycle times and ensures compliance with stringent OEM tolerances.
Food and Beverage
Factory automation helps maintain hygiene standards and consistency in production for packaged food and beverages. Applications include automatic bottling, carton forming, and weight-based sorting systems.
Packaging and Logistics
From palletisers to case erectors and barcode scanners, automated packaging lines are common in Malaysia’s logistics and FMCG sectors. Integration with warehouse management systems enhances traceability and inventory accuracy.
Benefits of Implementing Factory Automation
Companies in Malaysia invest in automation to remain competitive in regional and global supply chains. The main benefits include:
- Increased Productivity: Automation enables continuous operation with consistent cycle times, reducing dependency on manual labour.
- Improved Quality Control: Vision systems and in-line inspection tools minimise defects and ensure compliance with product specifications.
- Cost Efficiency: Over time, automation reduces operational costs by lowering labour expenses, rework rates, and energy usage.
- Enhanced Workplace Safety: Dangerous or repetitive tasks can be automated, reducing the risk of accidents and injuries.
- Data-Driven Decision-Making: Connected systems generate real-time data that support predictive maintenance and process optimisation.
Choosing a Factory Automation Solution Provider in Malaysia
Okaya Malaysia Sdn Bhd offers industrial clients access to factory automation components such as sensors, drives, and control systems sourced from global partners. While Okaya is not a system integrator, it serves as a reliable supplier supporting the automation needs of Malaysian factories with quality components and technical consultation.
Selecting the right automation partner is crucial to achieving ROI and ensuring system longevity. Key criteria for evaluating a solution provider include:
- Integration Experience: Providers should have proven deployment experience across similar industries and automation tiers.
- Component Portfolio: Access to a wide range of automation hardware and software from leading brands ensures flexibility.
- Technical Support: Ongoing training, troubleshooting, and system upgrades are essential for long-term system stability.
- Custom Engineering Capabilities: Ability to tailor systems to specific production workflows and space constraints.
- Compliance with Industry Standards: Solutions should align with ISO standards, SIRIM certifications, and occupational safety regulations.
Challenges in Factory Automation Adoption
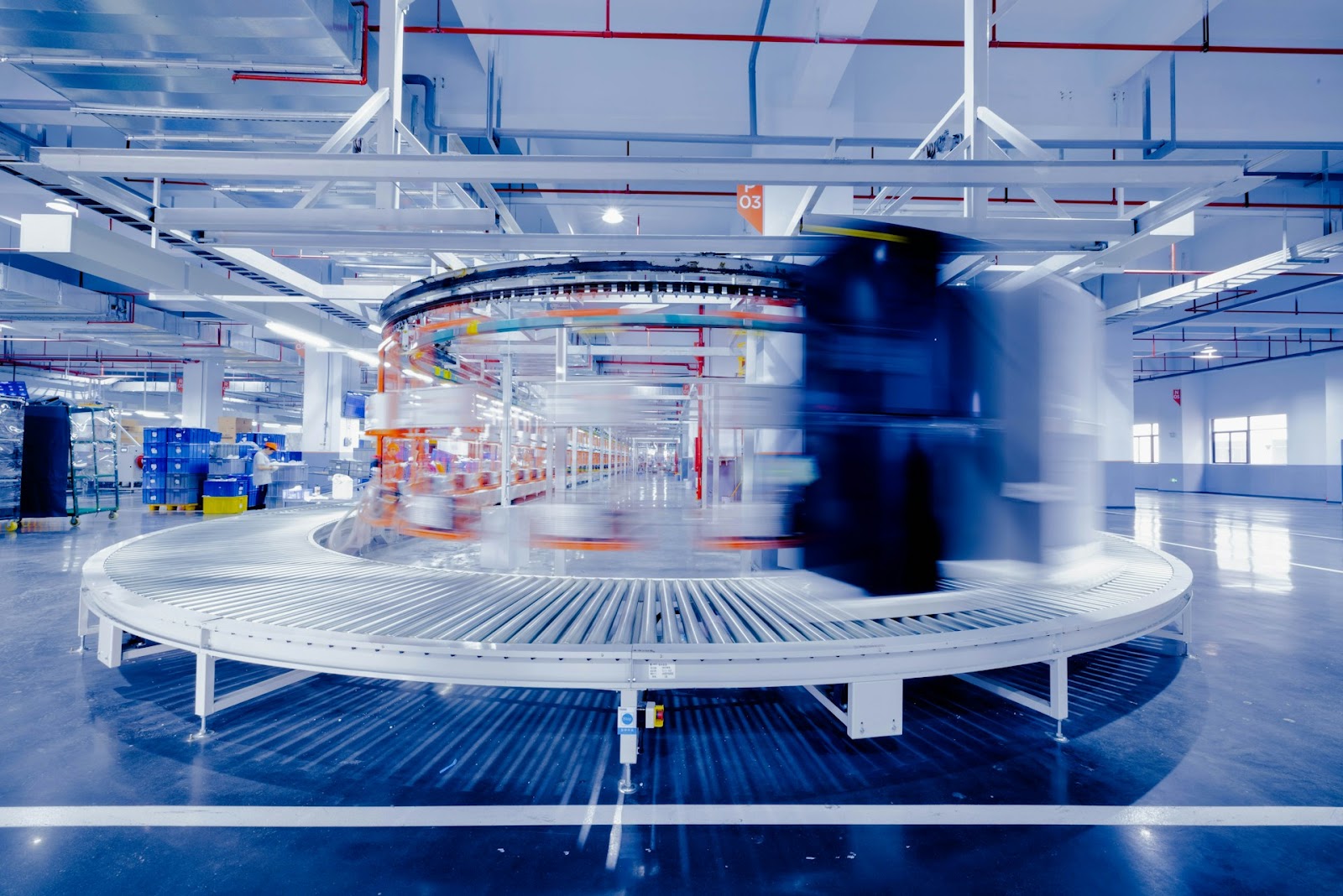
To address these challenges, some businesses begin with partial automation that focusing on high-impact areas. These are the several challenges that faced by the automation implementation in Malaysia:
- High Capital Expenditure: Initial setup costs for robotics, software, and infrastructure modifications may be prohibitive for SMEs.
- Workforce Reskilling: A skills gap exists in operating and maintaining automated systems, requiring investment in training.
- Legacy System Integration: Many factories operate older machines that require retrofitting or middleware for automation compatibility.
- Customisation Complexity: One-size-fits-all automation solutions often do not work in facilities with unique workflows or product variations.
Malaysia’s Factory Automation Outlook (2025–2030)
According to ResearchAndMarkets, Southeast Asia’s automation market is set to grow over 10% CAGR from 2024–2029, with Malaysia leading due to its strong manufacturing base and Industry4WRD-driven smart manufacturing investments.
Growth Drivers:
- Government Incentives: Grants and tax incentives provided by MITI and MIDA encourage automation upgrades, especially among SMEs.
- Labour Shortages: Rising wages and a shrinking industrial labour pool push companies toward automation as a long-term solution.
- Export Competitiveness: Automation improves production speed and quality—both critical for meeting global supply chain expectations.
- E&E Sector Growth: As Malaysia attracts more foreign investment in electronics and semiconductor assembly, automation becomes essential for scalability and precision.
Frequently Asked Questions
1. What types of factories benefit from automation in Malaysia?
Electronics, automotive, food processing, packaging, and general manufacturing facilities benefit most from automation due to volume, precision, and hygiene needs.
2. Is automation suitable for small manufacturers?
Yes. Scalable solutions such as modular robotics, sensor kits, and compact conveyors can help SMEs begin automating critical processes.
3. Can factory automation be integrated with ERP systems?
Yes. Most modern automation platforms support connectivity with ERP, WMS, or MES systems for end-to-end data integration and control.
4. What is the difference between factory automation and industrial robotics?
Factory automation encompasses a wide range of systems, including conveyors and control systems, while industrial robotics refers specifically to programmable robotic arms and machines.
5. Where can I find factory automation components in Malaysia?
Okaya Malaysia Sdn Bhd supplies automation hardware such as sensors, drives, and connectors, supporting system integrators and manufacturers across the country.
Factory Automation Solution Malaysia
Factory automation is an essential strategy for Malaysian manufacturers looking to increase competitiveness, reduce costs, and prepare for future production demands. Whether through robotics, smart sensors, or software integration, automation enables factories to operate at higher efficiency and with greater precision.
Choosing the right solution provider is key to successful implementation. Companies that work with trusted suppliers like Okaya Malaysia Sdn Bhd can access high-quality automation components, expert support, and scalable solutions tailored to Malaysia’s diverse industrial landscape.